Our Alcast Company PDFs
Our Alcast Company PDFs
Blog Article
The 8-Minute Rule for Alcast Company
Table of Contents3 Easy Facts About Alcast Company DescribedThe smart Trick of Alcast Company That Nobody is DiscussingThe Ultimate Guide To Alcast CompanyEverything about Alcast CompanyThe Only Guide to Alcast CompanyThings about Alcast CompanyThe 4-Minute Rule for Alcast Company
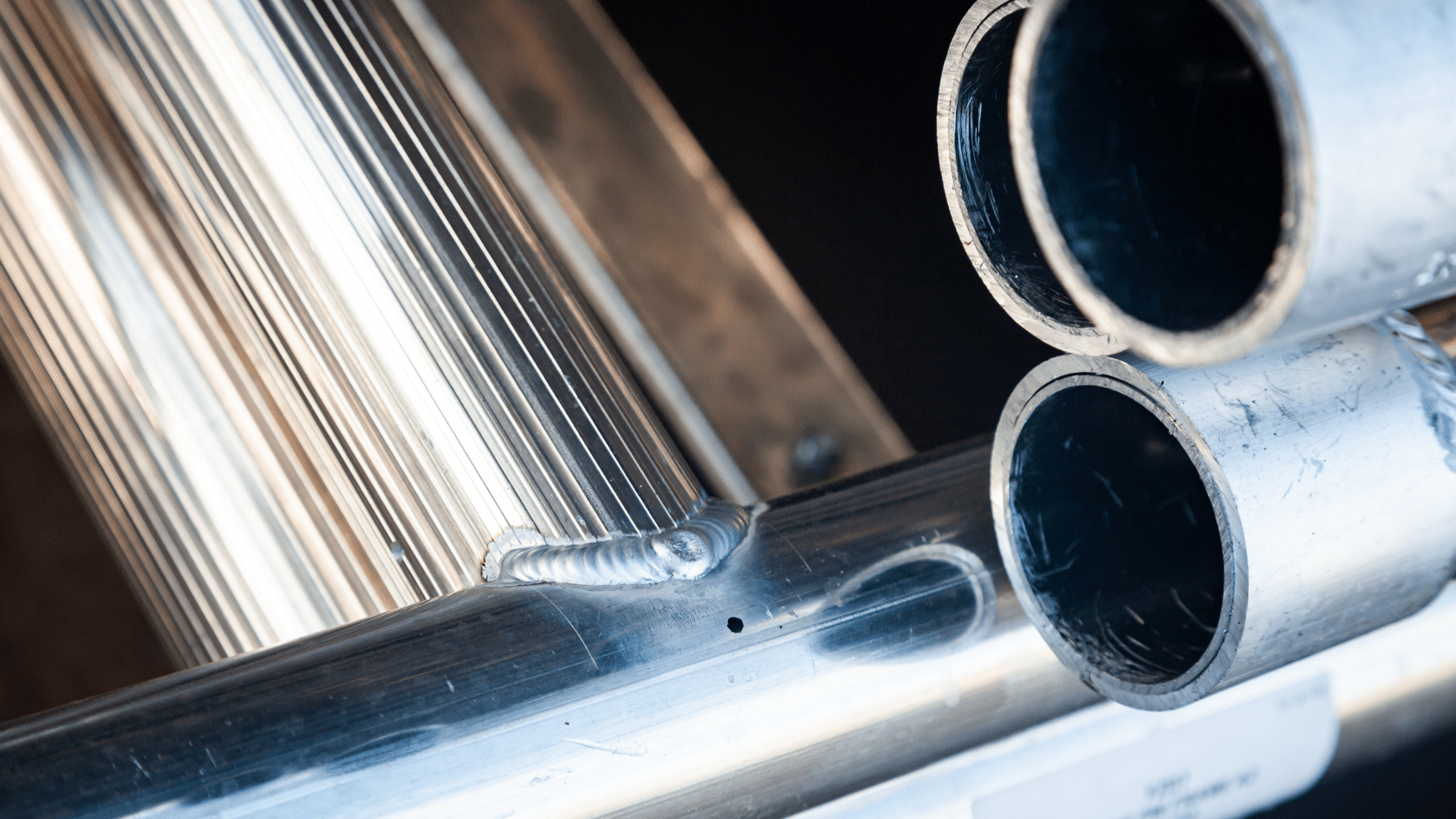
If you believe that a functioned alloy may be the very best for your job, take an appearance at several of our posts that discuss even more regarding certain functioned alloys, such as Alloy 6061 and Alloy 6063. On the other hand, if you think an actors alloy would be much better for you, you can discover more about some actors alloys in our Alloy 380 and Alloy 383 short articles (coming quickly).
Not known Details About Alcast Company
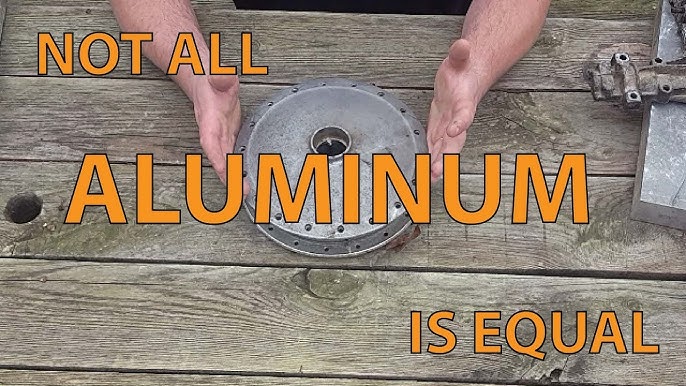
Having the experience and market expertise to engineer your spreadings for optimal production and quality end results will streamline the job. Producing light weight aluminum castings needs a complex collection of processes to attain the appropriate results. When choosing a brand-new light weight aluminum foundry to partner with, ensure they have extensive sector experience and are well-informed regarding all aspects of the light weight aluminum spreading procedure: style, production, material evaluation, and product testing.
(https://issuu.com/a1castcmpny)The factory should also have a tried and tested record of supplying remarkable items that satisfy or surpass consumer expectations. Quality assurance should also be at the top of your checklist when choosing an aluminum shop. By dealing with a certified foundry who complies with the criteria for quality assurance, you can protect the honesty of your item and ensure it satisfies your specifications.
The Ultimate Guide To Alcast Company
By selecting a business who offers solutions that fulfill or surpass your product needs, you can be sure that your task will certainly be finished with the utmost precision and efficiency. Various parts call for different production strategies to cast light weight aluminum, such as sand casting or die casting.
Die spreading is the name offered to the procedure of producing complex steel elements with use of molds of the part, likewise known as passes away. It produces more components than any type of other process, with a high degree of accuracy and repeatability. There are 3 sub-processes that fall under the group of die spreading: gravity die casting (or permanent mold casting), low-pressure die spreading and high-pressure die casting.
After the purity of the alloy is evaluated, passes away are developed. To prepare the passes away for casting, it is vital that the dies are clean, so that no residue from previous manufacturings remain.
The pure metal, likewise known as ingot, is added to the heater and maintained the molten temperature of the steel, which is after that moved to the injection chamber and injected right into the die (Foundry). The pressure is after that maintained as the metal solidifies. Once the steel solidifies, the cooling process begins
Our Alcast Company Diaries
The thicker the wall of the component, the longer the cooling time as a result of the quantity of indoor metal that additionally requires to cool. After the component is totally cooled down, the die cuts in half open and an ejection system pushes the element out. Complying with the ejection, the die is closed for the following shot cycle.
The flash is the extra product that is cast throughout the process. This need to be trimmed off using a trim device to leave simply the primary component. Deburring removes the smaller sized items, called burrs, after the trimming procedure. Ultimately, the element is brightened, or burnished, to provide it a smooth finish.
How Alcast Company can Save You Time, Stress, and Money.
Nonetheless, this showed to be an unreliable examination, since the tester can reduce right into a piece and miss out on a location with porosity. Today, top producers make use of x-ray screening to see the entire interior of parts without cutting into them. This permits them to extra accurately accept or deny components. To reach the ended up product, there are 3 key alloys used as die casting material to select from: zinc, light weight aluminum and magnesium.
Zinc is just one of one of the most used alloys for die casting as a result of its reduced price of raw products. It's additionally one of the stronger and stable steels. And also, it has superb electric and thermal conductivity. Its rust resistance additionally allows the components to be durable, and it is just one of the extra castable alloys due to its reduced melting factor.
Alcast Company for Beginners
As stated, this alloy is just one of the most generally utilized, yet makes will, sometimes, choose light weight aluminum review over zinc as a result of light weight aluminum's production benefits. Light weight aluminum is extremely affordable and one of the a lot more functional alloys. Aluminum is made use of for a variety of different products and industries anything from home window frameworks to aerospace materials.
Report this page